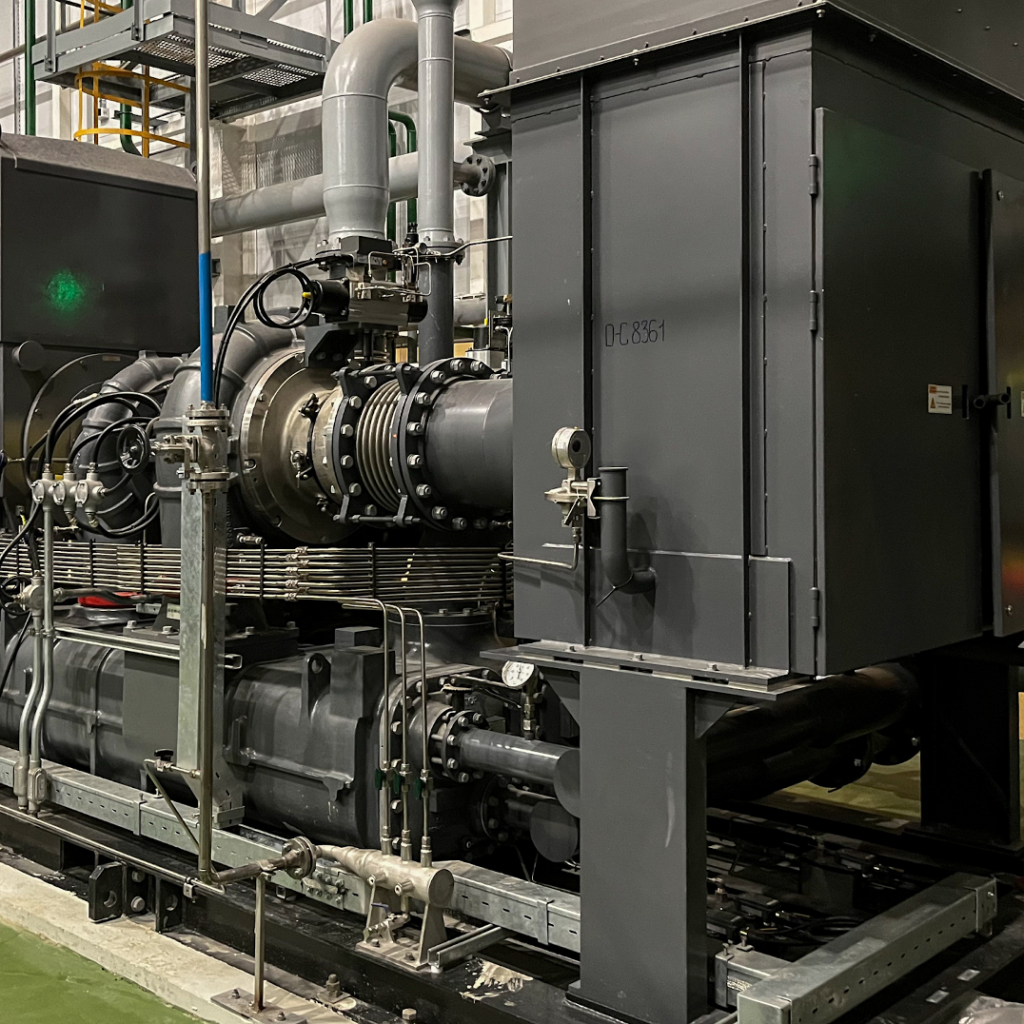
Air compressors serve as the unsung heroes in many industrial and commercial settings, providing the power behind a multitude of essential operations. To ensure these workhorses operate at peak efficiency, a proactive air compressor inspection checklist and maintenance schedule is indispensable.
In this guide, we’ll explore a comprehensive compressed air system maintenance checklist, shedding light on the key steps to enhance performance, prevent breakdowns, and extend the lifespan of this vital equipment.
Think of it as your preventative maintenance for air compressors checklist – helping you spot future risks and saving you costly urgent repairs.
1. Regular Inspection and Monitoring:
Check for air leaks, loose connections, and unusual noises. A simple method involves using an ultrasonic leak detector, soap solution, or an improvised method like listening for hissing sounds. Addressing air leaks promptly not only improves energy costs and efficiency but also prevents unnecessary wear on the compressor components.
Monitor pressure gauges for consistent readings within the specified range. Pressure gauges are the eyes of your air compressor system, providing vital information about its operational status. Sudden fluctuations or consistently low or high readings may indicate issues with the compressor or associated components.
Inspect belts and pulleys for wear and tension. Belts tensioning and pulleys wear and tear play a critical role in the functioning of many air compressors. Proper tension is crucial, as loose belts can slip and lead to reduced efficiency.
Additionally, check the alignment of pulleys and make adjustments as necessary. Routine inspections and timely replacement of worn-out belts contribute to smooth operation and prevent unexpected failures.
2. Lubrication:
Lubrication is the lifeblood of any machinery, and your air compressor is no exception. Manufacturers provide specific guidelines for lubrication intervals based on the type of compressor, its usage, its moving parts and environmental conditions. Strictly adhere to these recommendations to ensure optimal performance and longevity.
Overlooking or extending lubrication intervals can lead to increased friction, wear, and increase the chance of breakdowns.
Checking and maintaining the correct oil levels is a fundamental aspect of air compressor routine maintenance. Low oil levels can result in insufficient lubrication, leading to increased friction, heat, and premature wear of crucial components. Conversely, overfilling the oil reservoir can cause foaming, reduced lubricating efficiency, and potential damage.
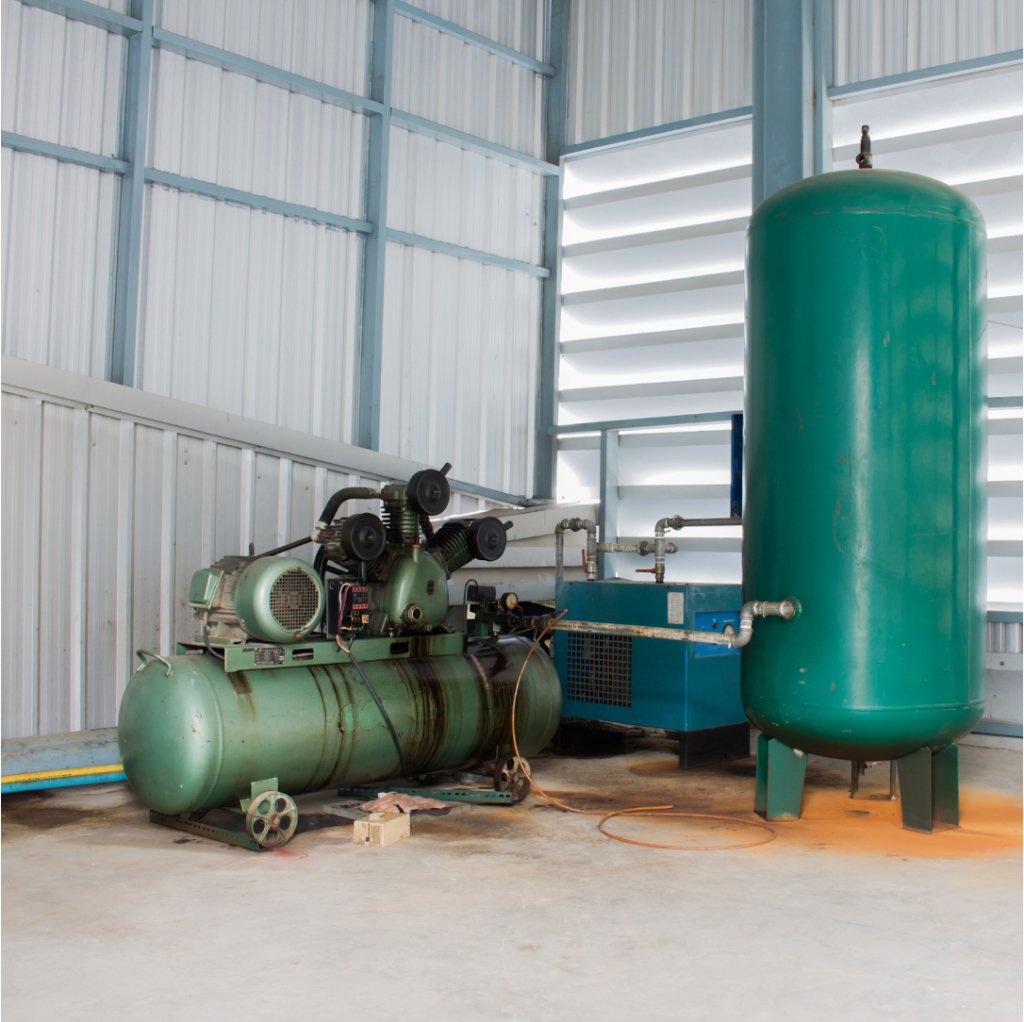
Any air compressor troubleshooting guide or checklist will tell you that regularly inspecting the condition of air compressor lubricants is crucial for identifying signs of contamination, degradation, oil leaks or depletion. Perform visual checks for the oil’s colour, consistency, and the presence of any foreign particles. If the lubricant appears discoloured or contains contaminants, it may be a sign that you need to replace the oil, before it gets to the point of risk for the machinery.
3. Air Filter Maintenance:
Air filters play a critical role in maintaining the purity of the air that enters your compressor. Over time, these filters accumulate dirt, dust, and debris, restricting the airflow and compromising the efficiency of the system. Inspecting the condition of your air filters and adhering to a routine cleaning or replacement schedule is one of the most important factors when it comes to compressor preventative maintenance tasks.
Ensure proper airflow to prevent strain on the compressor motor. Proper airflow is essential for the optimal functioning of your air compressor. A clean and unobstructed air filter allows the compressor to draw in air efficiently, preventing strain on the compressor motor, motor bearings and other components. Ensure that the filter housing is securely closed after cleaning or replacement to maintain a sealed and contamination-free environment.
By consistently cleaning or replacing air filters and ensuring proper airflow, you not only enhance the efficiency of your air compressor but also contribute to its longevity and reliability. A well-maintained air filter system protects your compressor from contaminants, reduces energy consumption, and ultimately results in cost savings for your operation.
4. Cooling System Check:
The cooling system of your air compressor is a critical component that helps regulate operating temperatures and prevents overheating. Regular inspection and cleaning of cooling system components are essential maintenance tasks to maintain optimal ambient temperatures.
Proper ventilation is crucial for maintaining optimal operating temperatures within the compressor. Inadequate ventilation can lead to overheating, reduced efficiency, and increased wear on components.
5. Inspect and Tighten Connections:
Electrical connections are the lifelines of your air compressor, facilitating the flow of power to critical components. Regular checks on electrical connections are vital for ensuring safety, preventing electrical malfunctions, and optimising performance.
Ensure that bolts, nuts, and fasteners are secure to prevent vibrations. Conduct vibration analysis on key components to identify potential areas of concern. Pay attention to components that experience higher levels of vibration, such as pistons, connecting rods, and motor mounts.
6. Drain Moisture from Air Tanks:
Moisture accumulation within air compressor tanks poses a significant threat to the internal components, leading to corrosion and potential system failures. Implementing a routine schedule for draining accumulated moisture is essential for maintaining the integrity and longevity of your air compressor.
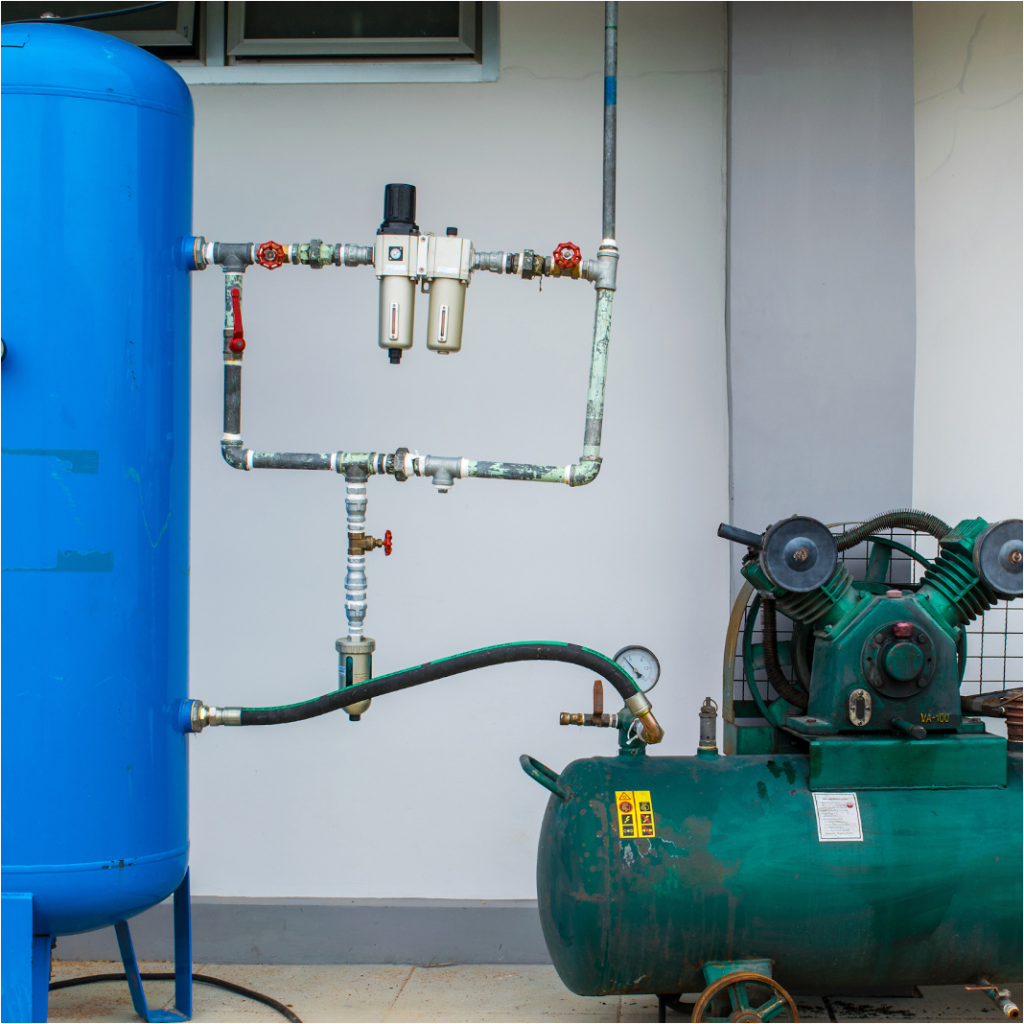
Install automatic drains if applicable for efficient moisture removal. While manual drainage is effective, installing automatic drains provides a proactive and efficient solution for moisture removal. Automatic drains operate based on preset conditions, enhancing the moisture removal process and reducing the likelihood of oversight.
7. Check Safety Systems:
Verify the functionality of safety features such as pressure relief valves. Pressure relief valves are critical safety components in an air compressor system, designed to prevent overpressurisation and protect both equipment and personnel.
Ensure emergency shutdown systems are operational. Emergency shutdown systems act as a crucial layer of protection, allowing for swift response in the event of an emergency or abnormal operating conditions.
8. Examine Belts and Pulleys:
Belts and pulleys play a crucial role in the transmission of power within your air compressor system. Regular examinations are essential to identify early signs of wear, misalignment, or tension issues.
Replace worn-out belts promptly to prevent damage to the compressor. Worn-out belts can result in reduced efficiency, increased energy consumption, and potential damage to the compressor components.
9. Inspect Motor and Controls:
Verify the motor’s performance and check for any abnormal vibrations. The motor is the powerhouse of your air compressor system, and its performance is crucial for overall functionality.
Examine electrical controls and ensure they are functioning correctly. Efficient electrical controls are essential for the safe and reliable operation of your air compressor system.
10. Evaluate Performance:
Regularly assess the compressor’s overall performance against its specifications. Routine evaluations of your air compressor’s performance against its specifications are fundamental to maintaining optimal efficiency and functionality.
Monitor power consumption and address any deviations. Power consumption is a critical aspect of compressor performance, and deviations from expected values may indicate underlying issues.
11. Recordkeeping:
Creating and maintaining a detailed log of all maintenance activities is a foundational practice for the effective management of your air compressor system.
Keep track of air and oil filter replacements, noting the type of filter used and the intervals between changes. This helps ensure that the filtration system consistently operates at optimal efficiency.
Whether through manual documentation or digital solutions, recordkeeping is an investment in the longevity and efficiency of your air compressor system.
Regular air compressor maintenance is not just a good practice; it’s a fundamental necessity for businesses reliant on compressed air systems.
It’s important to have routine air compressor maintenance, at PSI we do just that and will manage your maintenance schedule to save you time. Stay vigilant, follow manufacturer recommendations, and let your air compressor be a reliable cornerstone in your industrial endeavours.